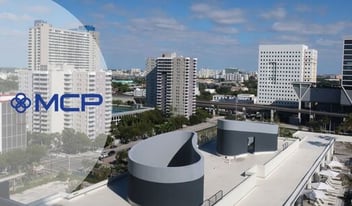
The Benefits of Emulsion Polymers in Recreational Surfaces: Enhancing Performance and User Experience
When it comes to organized athletic events, it’s hard to separate the venue from the sport and the play surface from the venue. In tennis, if you think of Wimbledon, you think of grass courts; if you think of the French Open, you think of red clay..
When it comes to organized athletic events, it’s hard to separate the venue from the sport and the play surface from the venue. In tennis, if you think of Wimbledon, you think of grass courts; if you think of the French Open, you think of red clay courts; and if you think of the U.S. Open, you think of hard courts. All of these surfaces provide a unique look and feel that contribute to that event’s mystique and charm. The surface, however, is not strictly an aesthetic concern — the nature of the surface affects the play of the respective sport, as well as the performance of the athletes.
Today, many tracks, courts, and other recreational surfaces, especially those at public parks, high schools, and universities, are synthetic surfaces made from rubber and ethylene propylene diene monomer (EPDM) granules bound together with a polymer, either polyurethane or a styrene-butadiene or acrylic emulsion polymer.
In this article, we will review how recreational surfaces are fabricated, the typical chemistries used, and their impact on athletic performance.
The Primary Types of Surface Systems
Recreational surfaces may appear as the smooth top layer that people see when they walk onto a tennis court, pickleball court, or playground, but there is more than meets the eye. In fact, what appears as a single layer is actually an entire surface system composed of many different layers working together to improve elasticity, durability, and user experience. This holds true whether the finished surface is natural or synthetic, because even natural surfaces require a solid substructure to function properly. Let’s review these two types of surfaces to understand how they offer different experiences to the user and affect the overall look and feel of the recreational area.
Natural surface systems, which have been used since the earliest days of organized sports, typically include cinder, clay, and grass.
- Cinder surfaces are made from scoria, a type of volcanic material that is both porous and lightweight. When it is crushed, the individual grains have tiny projections and spindles that lock together, making the surface firm and resilient. Cinder tracks offer more resistance than a synthetic track, which can be useful for athletes looking to improve running techniques or strengthen foot muscles.
- Clay surfaces feature either red or green colors based on their starting material. Red clay surfaces take their color from ground-up brick, while green clay surfaces take their color from crushed metabasalt, a type of metamorphic rock. Used primarily for tennis courts, clay surfaces are easier on joints and can actually prevent injury. They also create a slower and more defensive game because the rougher clay surface creates more friction on the ball.
- Grass surfaces make an appearance in running, tennis, and bike racing. While they offer a more natural look, they can be unpredictable, especially after they experience wear and tear. However, grass surfaces, because of their softer texture, are more forgiving on the joints of athletes and can even prevent impact injuries that occur on harder surfaces.
In general, all of these natural recreational surfaces require some regular upkeep and maintenance to keep them performing optimally and to prevent injuries in the people who play on them. Synthetics have emerged specifically to provide more consistent, cost-effective surfaces that also improve certain aspects of an athlete’s game. Synthetic surfaces are made using the following materials:
- Asphalt is made from bitumen — a black, highly viscous liquid or semi-solid form of petroleum that gets mixed with other aggregate particles, such as sand and stone, to form a hard, durable, and weather-resistant surface. In recreational surfaces, rubber may also be mixed into the bitumen. Asphalt surfaces are ideal for speed training and allow runners to maintain consistent speeds. In tennis, they contribute to faster ball speeds and more consistent bounces. Despite these advantages, they can be dangerous during extreme temperatures. Warm temperatures can heighten surface temperatures and burn or over-exhaust users, while cold temperatures can harden the asphalt.
- Polyurethane is a type of polymer made from two monomers, a diol and a diisocyanate. Because there is such a wide variety of these two monomers, polyurethane can take many forms, from a soft foam to a hard varnish. In recreational surfaces, polyurethane is used to bind crumb rubber pieces together into a flexible, durable mat. The finished surface provides good elasticity balanced with excellent endurance. It works well for outdoor tracks, which experience wide temperature extremes. And for athletes, it’s softer than asphalt, yet still provides firm footing for stability and speed.
- Styrene-butadiene (SB) is an emulsion polymer made by combining its two monomers in water. Like polyurethane, SB polymers function as a binder to hold rubber crumb together in an integrated surface. SB-based surfaces provide a soft landing that’s easier on joints and muscles — without sacrificing speed. Plus, these types of surfaces are permeable to water, so they drain quickly even after heavy rains.
Next, we’ll look at synthetic systems more closely to understand how most modern recreational surfaces are constructed.
Structure of Rubberized Synthetic Surface Systems
The history of recreational surfaces is directly linked to the International Amateur Athletic Federation (IAAF), which was founded in 1912 as the world governing body for the sport of track and field athletics. In 1989, the IAAF published their Performance Specification for Synthetic Surfaced Athletics Tracks (Outdoor). After a process of assessing various test methods and synthetic surfaces, the IAFF published a set of specifications and testing protocols for synthetic track surfaces. These guidelines have influenced how all modern tracks and courts are constructed.
Despite these guidelines, different installers use slightly different approaches to a synthetic surface installation. One approach relies on in situ methods, meaning that installers prepare and pour materials at the site where the tennis/pickleball court, track, or playground is located. For example, a paved-in-place surface consists of a base layer of polymer-bound black rubber granules, which is then topped with a spray-applied coat of polymer mixed with colored EPDM granules. Sandwich systems are similar. They start with the same black rubber base layer, but this layer receives a sealer coat before a layer of polymer is added. Finally, this is topped with EPDM granules.
Prefabricated surface systems are more expensive because they resist wearing better and require less maintenance than in situ surfaces. They consist of rubber mats that are manufactured in a controlled environment, which ensures that the finished surface has an even thickness and, as a result, more consistent performance. To install a prefabricated surface, workers adhere solid rubber sheets to a hard substructure with slot drains to keep the surface free of water. This kind of system produces a high-performing surface suitable for international athletics events, and it has been featured at major track and field championships and at Olympic venues.
No matter how a recreational surface is installed, the finished system has a distinct structure with alternating layers of materials, as shown below.
The Choice of Polymer: Polyurethane vs. Styrene-Butadiene Emulsion Polymer
All rubberized recreational surfaces rely on black rubber and EPDM granules. These elastomeric materials give the finished surface some bounce and even transfer energy to the feet of runners sprinting over the surface. It’s this particular feature that makes many modern tracks so fast and explains why so many world records have become vulnerable in recent years. For example, in the 2021 Tokyo Olympic Games, athletes raved about the bounce and energy return from the track and how it improved their performances. Many of them beat personal and Olympic records and recognized that the track surface system aided them greatly during their performance.
The polymer used in these surfaces also plays a major role. As we’ve already discussed, the two primary polymers used in synthetic surfaces are polyurethane and SB emulsion polymers. Both are used to bind rubber granules together, but they produce finished surfaces with different properties and different advantages and disadvantages. The table below compares recreational surfaces made from these polymers.
Polyurethane (PU)-Based Surface |
||||
Polymer Synthesis |
Initial Cost |
Long-Term Cost |
Durability |
Performance |
(In Organic Solvents) Diol + Diisocyanate + Catalysts + Additives |
$$$ |
$$ |
++++ |
++++ |
Styrene-Butadiene (SB)-Based Surface |
||||
Polymer Synthesis |
Initial Cost |
Long-Term Cost |
Durability |
Performance |
(In H2O) Styrene + Butadiene + Surfactant + Additives |
$$ |
$$$ |
+++ |
++++ |
As the table shows, polyurethane-based surfaces cost more to install, but they are more durable, especially in colder climates. SB-based surfaces cost less to install, but they may require more maintenance over the life of a track, tennis court, pickleball court, or playground. Both feature great performance characteristics and can help athletes run faster and jump higher.
Of course, rubberized tracks don’t need to be built from scratch. They can also provide a viable option to repair aging surfaces made from other materials. For example, asphalt tracks and courts can sometimes show rust spots and streaks. This occurs when pyrite-bearing aggregate, used as a component in the asphalt, begins to oxidize. As iron oxide is formed, brick-colored spots appear across the surface. These spots are not just eyesores — they also affect the quality of the surface. The rusty aggregates can form pits, which in turn can crack or crumble apart.
Maintenance staff have a few options to repair deteriorating asphalt. They can hire a contractor to drill out the visible iron pyrite and patch the holes with an acrylic patch binder, but this is time-consuming work. Another option is to cover the contaminated surface with a new course of asphalt, though this could result in similar problems if the asphalt is not sourced carefully to ensure a higher quality aggregate. A better option may be to apply an SB- or PU-based rubberized surface on top of the asphalt. Prefabricated systems are a popular because the rubberized mats can be applied directly over the previous surface. All of the pros and cons of SB versus PU apply to these repairs. SB surface repairs will be cheaper but may not last as long and may, because of their permeability, even become stained with rust after several years. PU surface repairs will cost more but should result in a longer-lasting surface.
Recreational Surfaces at Mallard Creek Polymers
Mallard Creek Polymers specializes in SB emulsion polymers. The flexibility of this copolymer allows for a wide variety of mixtures that can be matched to a specific need or requirement. For companies looking to enhance the performance features of their rubberized recreational surfaces, MCP is an ideal partner. We offer several off-the-shelf SB polymers that work well in all layers of a surface system — as a binder for rubber crumb and for EPDM granules and as the tack layers in between. Our SB emulsion polymers, Rovene® 4047, Rovene® 4125, Rovene® 4176, and Rovene® 4076, provide excellent adhesion, as well as flexibility and strength, for tennis and pickleball courts, running tracks, and playgrounds. We also offer Rovene® 6023, an acrylic emulsion polymer that can provide excellent abrasion and water resistance.
If you need to go beyond our standard SB emulsion polymers, we can collaborate with your team to design a custom SB solution or consider additional chemistries, such as acrylics, vinyl acetate ethylene (VAEs), nitriles, and polyurethane dispersions (PUDs). We have extensive experience working with both recreational surfaces and other types of rubberized surfaces, such as mats used in industrial, construction, agricultural, or landscaping settings. We have also developed solutions for tangentially related applications. For example, MCP offers an SB emulsion polymer for soil stabilization, which is primarily used for dust suppression.
Regardless of your specific end use or application, you will find working with MCP is a different experience. We work as your partner throughout the entire development process and offer expert insight into the right products for your finished system. For more information visit the Mallard Creek Polymers website and speak to one of our chemists about designing your next recreational surface system.
