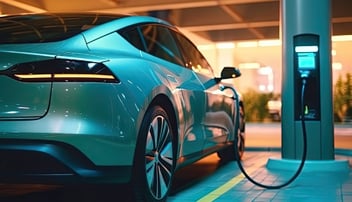
For decades, manufacturers relied on mechanical fastening solutions when they needed to attach one material to another. For example, furniture makers used tacks to attach leather to wood. And shoemakers used thread to attach leather to leather and..
For decades, manufacturers relied on mechanical fastening solutions when they needed to attach one material to another. For example, furniture makers used tacks to attach leather to wood. And shoemakers used thread to attach leather to leather and leather to the sole. Then, in the 20th century, synthetic materials emerged as viable alternatives for both the construction of finished products and, in the form of adhesives, for bonding various elements together.
Today, contact adhesives are vitally important to many manufacturing processes. They are typically non-bonding when contacting other surfaces, but they aggressively bond to themselves upon contact — a property known as auto-adhesion — leading to extremely strong and permanent bonds. In addition to bond strength, contact adhesives are desirable because they can be formulated to have long open times, which means adhesive-coated substrates do not need to be combined for several minutes.
Contact adhesives are ideal for a variety of laminating applications, where they can be used to bond large areas of non-porous substrates. For example, in furniture making, they are used extensively on kitchen and bathroom countertops to bond plastic laminates to wood or particle board. In construction, they are used to attach roofing membranes to their substrates. They can also be used in smaller areas, such as in footwear construction to attach uppers, soles, linings and other components, as well as in the automotive industry to attach automotive trim.
Many contact adhesives today are based on polychloroprene, but as the cost of polychloroprene fluctuates globally due to evolving market conditions, adhesives manufacturers are searching for cost-effective alternatives that still deliver high performance. This blog will explore contact adhesives and will review how other chemicals, such as emulsion polymers from Mallard Creek Polymers, can either improve the properties of polychloroprene-based adhesives or extend the life of polychloroprene supplies by replacing a certain portion of the chemical in a specific formulation.
One-part vs. Two-part Systems
An important concept related to contact adhesives is curing, which refers to the chemical process in which the adhesive fully crystallizes. As this occurs, it attains its final properties and builds up its final strength. The time it takes to complete crystallization is known as cure time.
Contact adhesives come in either one-part or two-part systems based on how they cure. One-part adhesives, as their name implies, are comprised of a single component that cures on its own without the need for a second component. Instead, one-part adhesives require an external chemical or energy source to initiate curing. These external sources include moisture, heat and light. For example, hot melts must be heated, while reactive hot-melt urethanes require both heat and atmospheric moisture for curing.
Two-part adhesives describe any adhesive that needs two parts to be mixed in order to cure. These adhesives are sometimes called reactive adhesives because curing is dependent on a chemical reaction. To ensure that this reaction takes place fully, it is absolutely essential for the two required components to be dosed in the correct mixing ratio and for them to be evenly mixed. Mixing can occur before the adhesive is dispensed, or some manufacturers package the two components into special cartridges with static mixers that mix the product as it is gunned.
Although one-part adhesives would seem to offer advantages because of their ease of preparation, the choice of adhesive should be based on the application and the environment where the adhesive will be used. Two-part adhesives have a faster cure time and are generally stronger than one-part adhesives. They are also more flexible and will bond almost anything. Finally, two-part adhesives have an extended shelf life compared to one-part options, which must be protected against moisture, heat and light.
Polychloroprene-based Contact Adhesives
Contact adhesives are formulated by dissolving a rubber in a liquid dispersion system. Typically, the rubber is polychloroprene, or chloroprene rubber, which was introduced by DuPont in 1931 as the first synthetic rubber. Originally sold under the name Duprene, polychloroprene was renamed Neoprene, which remains one of the most important specialty elastomers with an annual consumption of 300,000 tons worldwide.
One type of formulation has the polychloroprene rubber dissolved in a solvent, such as toluene, hexane, methyl ethyl ketone, xylene or methylene chloride. Solvent-based polychloroprene adhesives deliver immediate green strength (the early development of bond strength) and excellent ultimate bond strength. Their properties can also be easily tweaked to have long or short open times (the time after an adhesive is applied during which a serviceable bond can be made), high-temperature bond strength and ultimate peel and shear strength. Plus, the cured adhesives are generally resistant to heat, oxidation, water, solvents and other chemicals. Unfortunately, the solvents used in the formulations can produce hazardous air pollutants and can produce vapors that may be flammable in certain conditions.
Water-based formulations for polychloroprene adhesives are also possible to mitigate the environmental, health and safety profile of the adhesive. Historically, these water-based systems offered inconsistent bonding properties, with long dry times and slow development of bond strength. The stability of these systems, however, has improved over the years.
Extenders for Polychloroprene Adhesives
Formulators often take advantage of extenders for two reasons — to control costs as the global polychloroprene market fluctuates and to improve the performance properties of polychloroprene adhesives. The use of fillers and extenders can affect certain properties, so it's important to balance the expected improvements against possible property decline.
Styrene-butadiene (SB) extenders are one class of chemicals that can be used in formulation with polychloroprene. Non-carboxylated SB latex polymers improve green strength and offer excellent adhesion to foam, providing flexibility to the foam bond without hindering application, which occurs typically through sprayers. SB polymers can also be stabilized with rosin to impart certain desirable properties. Rosin is a naturally occurring resin derived from pine and spruce trees, either by treating sap (for gum rosin), by extracting from pine tree stumps (for wood rosin) or by removing one of the byproducts of wood pulp manufacturing (tall oil rosin). Rosin consists of acidic molecules, including abietic-type acids, and can function effectively as the surfactant in the emulsion polymerization of styrene-butadiene, producing a tackification effect that improves the performance of sealants, hot melts and adhesives.
Acrylic polymers can also be used as extenders. They are extremely compatible with polychloroprene dispersions and offer excellent sprayability. They also provide toughness and high-temperature bond performance.
Contact MCP for Contact Adhesives Support
Mallard Creek Polymers (MCP) currently offers a number of solutions for partial replacement of polychloroprene in adhesive formulations. These include two non-carboxylated styrene-butadiene emulsion polymers: Rovene 4848 (Tg –38°C), specifically designed for the use in a two-part spray adhesive for open or closed cell foams and other contact and cold seal applications, and Rovene 4220 (Tg -26°C), recommended for cold seal applications. Also included are styrene-acrylic polymers with higher glass transition temperatures, high strength and good adhesion to multiple substrates: Rovene 6133 (Tg +10°C), Rovene 6034 (Tg +23°C), and Rovene 6026 (Tg +20°C).
MCP is also actively working on polychloroprene-free polymer solutions for contact adhesives, based primarily on styrene-butadiene and acrylic chemistries. In addition to reducing the use of polychloroprene in contact adhesives, MCP can help with formulations for all of your sealant and adhesive needs, including pressure-sensitive adhesives, laminating adhesives, construction adhesives and removable adhesives. We’re a small, attentive specialty manufacturer who works closely with our customers to customize the properties of our emulsions to meet specific application requirements.
Contact MCP today to discuss your adhesive project needs.
