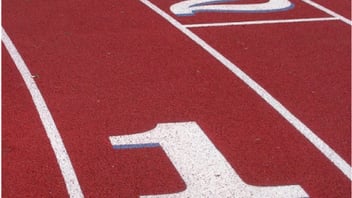
Concrete is the single most widely used material in the world. It’s strong, durable and versatile, capable of being formed into almost any shape. This makes it an ideal material for the construction of foundations, roadways, bridges, tunnels, dams,..
Concrete is the single most widely used material in the world. It’s strong, durable and versatile, capable of being formed into almost any shape. This makes it an ideal material for the construction of foundations, roadways, bridges, tunnels, dams, skyscrapers and more.
But concrete isn’t impervious to the elements. One of the most critical challenges facing concrete structures today is moisture penetration. Water damage can include deterioration and corrosion caused by alkalis, salts and acids. It can also promote the growth of toxic mold and mildew, which puts the entire structure at risk.
The best way to prevent water intrusion is to protect concrete structures through a process known as structural waterproofing. Structural waterproofing is largely associated with basements and below-ground structures, but it can be used in both interior or exterior and above- or below-grade situations. The process typically begins with a thorough analysis of the construction site, the materials used and the types of conditions likely to be encountered. Engineers then develop a specific plan such that the structure in question will remain unaffected by water or will be able to resist the ingress of water across a set of carefully defined specifications.
A key part of the plan requires selection of an appropriate waterproofing solution. There are a number of solutions available, but here we review three of the most common.
Bituminous materials — Bitumen, also known as asphalt, is a mixture of organic liquids that are highly sticky, viscous, and waterproof. When applied to structures, especially the roofs of buildings, they can provide an effective water barrier. They can also be enhanced with polymers to decrease drying times and increase resistance to hydraulic pressure. But bitumen also has several disadvantages. For example, exposure to extreme heat and UV radiation drastically decreases the lifespan of bitumen waterproofing systems.
Liquid waterproofing membranes — Liquid membranes are polymer-based systems that are applied by hand, using a roller or trowel, or by spraying onto exposed surfaces. They offer a number of advantages, such as their ease of application and their flexibility to expand and contract as the temperature changes. The biggest benefit of liquid membranes, however, is that they cure into a seamless rubbery coating, with no seams or joints to allow water ingress.
Cementitious coatings — Cementitious coatings, as the name implies, rely on cement-based coatings to provide a waterproof barrier. These systems combine Portland cement with a waterproofing agent, typically a synthetic emulsion polymer. They can be applied behind tile, over masonry patching and over concrete surfaces. Cementitious coatings are popular because they’re easy to apply, create breathable barriers and offer superior bonding strength. Plus, they function equally well in both above- and below-grade applications.
1K and 2K Cementitious Waterproofing
Cementitious coatings can be classified either by the surface onto which they’re applied or by the number of components used in the system. In the former category, cementitious coatings can give concrete and masonry surfaces positive- and negative-side waterproofing. A positive-side surface refers to the surface exposed to positive hydrostatic pressure — i.e., the water pushes the barrier against the structure. A negative-side surface is just the opposite — i.e., the water tries to pull the barrier away from the structure. On a foundation, for example, the positive-side surface would be the outside surface closest to the soil. The negative-side surface would be the inside surface of the basement wall. Cementitious coatings can also be classified as either 1K (one-component) or 2K (two-component) systems.
1k Systems
In 1K systems, systems, a dispersible powder gets mixed with some type of hydraulic binder (most often Portland cement), well-graded sand or other aggregates and various powder additives. This mixture is supplied prebagged by the manufacturer and combined with water at the construction site prior to application. Once mixed, the cementitious material can be brushed, troweled or sprayed onto surfaces. This makes 1K systems extremely easy and convenient to use for both indoor and outdoor applications. Most formulations are resistant to negative-side hydrostatic pressure, so they are ideal for interior waterproofing of below-grade foundation walls.
2k Systems
In 2K systems, there are two premixed components. The powder component contains mainly quartz sand, cement, and various additives, including thickeners and hydrophobic agents. The liquid component consists mainly of a specially designed polymer dispersion with excellent cement compatibility. Like 1K systems, 2K systems can be brushed, troweled or sprayed onto either horizontal or vertical surfaces, so they, too, are considered easy, convenient waterproofing solutions.
Synthetic emulsion polymers are ideal for 2K cementitious waterproofing membranes. They provide a tough but flexible/elastomeric membrane suitable for both positive- and negative-side waterproofing of interior and exterior concrete and masonry surfaces. The elasticity of the material prevents it from shrinking and enhances its crack-bridging properties. In fact, it forms what is known as tenacious adhesion — a fully adhered monolithic, seamless, rubber-like membrane that can bond to many different surfaces. And 2K latex membranes deliver all of this while still allowing the concrete to breathe and remaining APEO- and VOC-free.
For all of these reasons, 2K cementitious systems are great waterproofing solutions for all wet areas, such as bathrooms, swimming pools, terraces, kitchens, water tanks and balconies. They are also appropriate for garage slabs, basement walls and, in industrial settings, for utility pipes, underground tunneling, flat roofs and storage tanks and reservoirs.
Polymer Partners
Mallard Creek Polymers specializes in the design and manufacturing of emulsion polymers for a wide range of applications, including polymer-based waterproofing solutions. We work with customers to understand their design and engineering challenges and to develop emulsion polymers that address those needs, tweaking properties based on the intended application. Contact us for more information.
