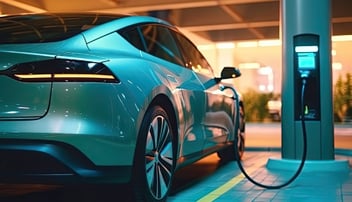
Choosing a polymer for your project: carboxylated or non-carboxylated? Carboxylated latexes are the most widely used of all commercial latexes. When selecting the best emulsion polymer for your project, however, why would you choose a carboxylated..
Choosing a polymer for your project: carboxylated or non-carboxylated?
Carboxylated latexes are the most widely used of all commercial latexes. When selecting the best emulsion polymer for your project, however, why would you choose a carboxylated polymer over a non-carboxylated polymer? It comes down to one property: adhesion.
Paint is a good example of an application demanding a coating that bonds well to the substrate and that can be expected to remain bonded for years. Peelable protective films and stickers such as name tags, on the other hand, should release easily.
What Is Carboxylation?
In emulsion polymerization, chemists mix monomers, initiators, and surfactants into water. Surfactant molecules aggregate together, forming nano-micelles and helping to stabilize micro-monomer droplets. As initiators are added, polymer formation begins, and micelles grow as monomers migrating into them.
This basic process was developed and refined in the 1920s. After this era, chemists explored how to modify emulsion polymers even further. Carboxylated latexes were invented in the 1940s as a means to balance some of the negative effects of surfactants, especially in many coating applications. Free surfactant in particular — the portion of surfactant that doesn’t bond to the polymer chains — tends to agglomerate between polymer chains and aggregate at surfaces, which degrades moisture sensitivity.
Carboxylation involves adding a strong acid monomer, such as acrylic acid (AA), methyl methacrylate acid (MMA), itaconic acid (IA), or fumaric acid (FA), in the polymerization reaction. This stabilizes micelle formation and reduces the amount of surfactant needed.
Many different factors affect carboxylation, and chemists can manipulate these factors to formulate a wide variety of products to meet the specific needs of the application by:
- Selecting from a variety of carboxylic monomers that provide different degrees of hydrophilicity (attraction to water). For example, MMA provides the lowest degree of hydrophilicity, while AA, IA, and FA provide greater degrees of hydrophilicity.
- Controlling the degree of neutralization, or ionization, used during the polymerization process.
- Managing when and how the carboxylic monomers are added during the process — for example, early, late, continuously, or as a “single shot” addition.
- Using more water-soluble comonomers, such as MMA or acrylamide, as coupling agents.
- Controlling the latex particle size, which affects the quantity of carboxylic groups on the particle surface — the smaller the particle size, the more carboxylic groups will form on the particle surface.
Carboxylation also adds cross-linking capability to the polymer — the degree to which the polymer chains join to one other — which can be measured by the “acid number.” A high acid number indicates more carboxylic acid groups, quantifying the amount of acid present.
If you visualize a polymer as a single strand or chain, cross-linking weaves these strands together, increasing strength and toughness. The cured coating will exhibit more hardness and gloss than a non-cross-linked emulsion polymer-based coating.
A carboxylated polymer emulsion provides improved resistance to grease, solvents, abrasion, heat, and UV, and carboxylation enhances its pigment binding capacity. Perhaps most importantly, a carboxylated polymer provides good adhesion to a substrate, and this adhesion will increase over time to the formula.
Carboxylated vs. Non-carboxylated Polymer Latex Emulsions
Since their development, carboxylated latexes have become increasingly popular for various applications — they amount to more than 90 percent of all the commercial latexes. With excellent water resistance, good adhesion, and high strength and elasticity, carboxylated latexes are most appropriate for coatings for metals, plastics, and glass, as well as for applications in paper and non-woven coatings.
Even still, non-carboxylated latexes have their place as commercially viable products and provide multiple advantages. For example, non-carboxylated latexes are ideal for:
- Certain cement-based applications requiring the absence of a carboxylic group.
- Spray adhesives and beater addition processes used in papermaking, where the lower stability of the emulsion polymer allows it to deposit rapidly on substrates.
- Temporary protective coatings, such as film-type products and removable adhesives used in stickers or decals, which requires stable adhesion that does not increase over time.
Consider the Application Requirements
When selecting a latex emulsion, the formulator must consider the properties needed in the end product, particularly the level of adhesion. By managing the level of carboxylation, Mallard Creek Polymers can tailor adhesion and other properties like water resistance and hardness to meet the specific application requirements in a custom polymer solution.
