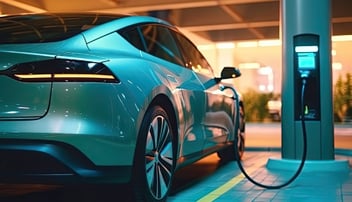
Ambient Cure Acrylic Emulsion Polymers Utilizing DAAM/ADH Technology
Solvent-based polymer systems are giving way to water based acrylic polymer emulsions due to environmental concerns and related regulations limiting volatile organic compounds (VOCs), as well as a desire to achieve significant improvements in the..
Solvent-based polymer systems are giving way to water based acrylic polymer emulsions due to environmental concerns and related regulations limiting volatile organic compounds (VOCs), as well as a desire to achieve significant improvements in the performance characteristics of the water-based emulsion polymers.
Emulsion polymers are the system of choice for several product classes:
-
Paints and Coatings
-
Printing and Packaging
-
Waterproofing membranes
-
Textiles and nonwovens
-
Adhesives and sealants
Waterborne acrylic polymers have seen advancements in film mechanical properties; chemical, water, and abrasion resistance; durability; adhesive properties; and solvent resistance. New developments in polymer crosslinking chemistries have contributed to this array of performance enhancements.
The leading crosslinking technology—crosslinking chemistry based on diacetone acrylamide (DAAM) and adipic acid dihydrazide (ADH)-- is known as keto-hydrazide crosslinking.
Advantages of the DAAM/ADH Crosslinking System
There are multiple considerations related to the DAAM-ADH crosslinking system that provide many benefits for consumers:
-
DAAM and ADH are safe to use.
-
Both are easy to use for a variety of formulations.
-
Neither DAAM nor ADH contains formaldehyde.
-
Diacetone acrylamide uniformly copolymerizes within acrylic copolymers, creating well-dispersed pendant ketone crosslinking sites.
-
Waterbased acrylic emulsions based on diacetone acrylamide with ADH in the aqueous phase, are initially non-reactive and afford emulsion polymers with good long-term stability for easier shipping and storage in retail containers.
-
After film coalescence, crosslinking becomes rapid at ambient temperatures, thanks to water evaporation in the drying process and a simultaneous reduction in pH arising from the loss of ammonia.
-
Because crosslinking is post-coalescence, the resulting three-dimensional polymer network exhibits maximum film cohesive properties, as well as enhanced mechanical strength and durability.
-
Crosslinking with the keto-hydrazide chemistry enhances some key attributes, including abrasion, scrub, stain, and blocking resistance; moisture and solvent resistance; and substrate adhesion.
With other crosslinking chemistries, premature crosslinking occurs within the emulsion particles prior to coalescence. This process slows intermolecular diffusion between emulsion particles, resulting in weaker film products and coatings. The likelihood of this scenario increases when diacrylates are used in the copolymerization recipe to produce crosslinks.
With the keto-hydrazide chemistry, crosslinking occurs post-coalescence. This dynamic enables good molecular inter-diffusion between emulsion particles as the film dries, which enhances film properties.
The Chemistry of DAAM/ADH Crosslinking Monomers
The circled moieties in the chemical structures below highlight where the crosslinking happens with these two molecules:
The diacetone acrylamide monomer is soluble in water and most organic solvents. This quality enables DAAM to be easily incorporated into polymerization recipes.
DAAM free-radical copolymerization can post-react with ADH to form ambient cure systems. DAAM can also effectively be copolymerized with vinyl acetate monomer, MMA, acrylic esters, acrylamide, styrene, and others—whether in solution, bulk, or emulsion systems.
ADH, as a difunctional crosslinking agent, has a melting point of 177–184°C and is moderately soluble in water. Here’s a view of its structure:
After adding ADH to an ammonia-neutralized acrylic emulsion containing DAAM, the emulsion remains stable when stored in one pot.
Applications for Ambient Cure Acrylic Emulsions
Perhaps the most significant attribute of ambient cure pure acrylic emulsions is their versatility. Formulators can use these systems in multiple applications across a variety of industries.
Since the advent of these ambient cure all acrylic polymers, we’ve seen the greatest adoption in the paints and coatings industry. Among modern paints and coatings utilizing DAAM/ADH are durable interior and exterior coatings for architecture, wood, and concrete.
If you are seeking an ambient cure all acrylic polymer emulsion, contact Mallard Creek Polymers today.
Polymer scientists utilize DAAM and ADH monomers to develop ambient cure polymers which optimize the mechanical properties, and to achieve good stain resistance, toughness, impact resistance, scrub resistance, adhesive properties, and more for a variety of marketplace applications.
If you’re ready to take advantage of the benefits of these ambient cure acrylic polymers for your coatings applications, our team at MCP is ready to help. We can provide information on the ambient cure acrylic polymer emulsions in our portfolio and provide the technical support to help you optimize your product formulations moving forward.
